Sommaire
Contextualisation
Définitions synthétiques
Un robot industriel est une machine manipulatrice à plusieurs degrés de liberté, programmable, polyvalente et contrôlée automatiquement, destinée à être utilisée dans des applications d’automatisation industrielle. Il peut être soit fixe, soit mobile.
- Les robots mobiles sont des robots industriels automatiques programmables se déplaçant librement.
- Les robots prothétiques sont des manipulateurs ou des dispositifs programmables pour les membres humains manquants.
Un cobot est un robot capable d’être utilisé dans une opération de collaboration avec un opérateur humain.
Un espace de travail collaboratif est un type particulier d’opération dans lequel un opérateur et un robot partagent le même espace de travail.
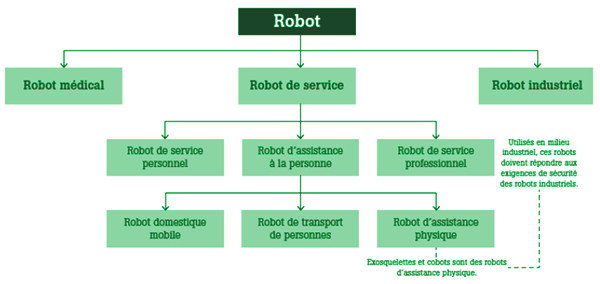
Classification des robots de l’INRS (Atain-Kouadio et col., 2015)
(Pour une définition plus complète aller ici)
Concepts et normes encadrant la sécurité des robots / cobots
La hiérarchie de sécurité repose sur 3 niveaux :
- L’élimination, qui consiste à supprimer physiquement un danger.
- Les contrôles techniques, qui comprennent la programmation, les barrières de sécurité …
- Les règles organisationnelles / contrôles propres à l’entreprise, qui modifient la façon dont un opérateur travaille par le biais d’instructions de travail, de restrictions, etc.
Exigences de sécurité relatives aux robots industriels
Norme NF EN ISO 10218 partie 1 et partie 2
Tous les robots utilisés au travail doivent répondre aux exigences de la norme NF EN ISO 10218 partie 1 et partie 2 de 2011 qui définissent les exigences de sécurité relatives aux robots industriels.
- La norme ISO 10218-1:2011 partie 1 traite des éléments essentiels de sécurité pour les robots industriels.
- La norme ISO 10218-1:2011 partie 2 intègre les exigences de sécurité au niveau de l’intégrateur.
Celles-ci indiquent les principes techniques combinables entre eux et à choisir en fonction de la situation :
- L’arrêt nominal de sécurité contrôlé ;
- Le guidage manuel ;
- Le contrôle de la vitesse et de la distance de séparation ;
- La limitation de la puissance et de la force du robot en cas de contact.
Ces solutions techniques doivent être associées à des solutions organisationnelles :
- Actions de formation : développement de nouvelles compétences liées à la mise en œuvre du cobot (y compris éventuellement prise en charge de la maintenance de premier niveau) ;
- Suivi d’activité : évaluation et évolution des sollicitations physiques et psychosociales;
- Changement d’organisation : adaptation du travail demandé, modification du poste de travail, réaménagement et réorganisation du travail collectif.
Autres normes importantes :
- La norme ISO/ TS 15066-2016 s’appuie sur les deux normes précédentes et fournit des exigences de sécurité pour les robots industriels collaboratifs.
- L’Association des Industries de la Robotique (RIA) a rédigé un rapport technique en 2016, le RIA TR R15.606-2016 qui renforce la sécurité du personnel avec les systèmes de robots industriels collaboratifs. Il s’articule autour de deux concepts centraux, à savoir la conception de systèmes de robots collaboratifs et les exigences en matière d’applications.
- Les normes ISO 13850 et ISO 13855 traitent des fonctions d’arrêt d’urgence et du positionnement des dispositifs de protection en fonction de la vitesse d’approche d’un corps humain.
- La norme CEI 60204-1 comprend des exigences générales pour les équipements électriques utilisés dans les machines.
Repenser la prévention des risques tout au long de la démarche d’intégration
Pour l’étape d’identification des risques, les fabricants et intégrateurs peuvent s’appuyer sur la norme NF EN ISO 12100 Sécurité des machines – Principes généraux de conception – Appréciation du risque et réduction du risque.
Dans le cadre de la mise en œuvre d’une cellule robotique collaborative, compte tenu de la proximité immédiate de l’opérateur avec le robot, certains risques doivent bénéficier d’une attention particulière.
La coactivité entre hommes et robots collaboratifs implique de repenser la prévention des risques tout au long de la démarche d’intégration et impose la prise en compte de l’ensemble de ces risques par la mise en place de principes techniques accompagnés de mesures organisationnelles.
Comme n’importe quelle machine, ces robots comportent des éléments en mouvement (bras, pinces, outil, pièce manipulée) susceptibles d’engendrer :
- Des risques d’impacts physiques (écrasement, choc …) ;
- Des risques spécifiques en fonction des outils et de la nature des tâches réalisées (brûlures, intoxications, vibrations …)
À ces risques peuvent s’ajouter des contraintes physiques et psychiques à l’origine notamment de :
- Troubles musculosquelettiques (TMS) : douleurs aux membres supérieurs, poignets, dos …
- Risques psychosociaux (RPS) : surcharge mentale, stress, isolement, fatigue…
Risques | Origines | Conséquences |
Risques liés aux impacts physiques | Mouvement (bras, pinces, outil, pièce manipulée) dans l’espace d’évolution de l’opérateur. Chute ou éjection de pièces ou produits… | Écrasement Cisaillement Coupure ou sectionnement Choc Perforation ou piqûre Friction, abrasion Dommages neurobiologiques Désordres vasculaires |
Risques Spécifiques | Contact avec des éléments chauds ou froids. Température excessive liée au processus Contact avec des produits chimiques… | Brûlure (chaude ou froide) Lésion (yeux, peau) produite par rayonnement Intoxication (dégagement de gaz, fumées, poussières) |
Troubles Musculosquelettiques (TMS) | Contraintes physiques et psychosociales dues à l’interaction homme-robot Contact avec des éléments vibrants (guidage manuel par exemple) | Douleurs aux poignets, épaules, coudes, nuque, dos |
Risques psychosociaux | Contraintes psychiques liées aux risques potentiels de chocs (ou contacts répétés) Contraintes psychiques liées aux activités de surveillance / contrôle Dépendance de l’opérateur au rythme du robot Poste de travail inadapté Fragilisation des collectifs Isolement social Monotonie du travail | Fatigue Stress Surcharge mentale |
Le tableau ci-dessus liste les principaux risques associés aux interactions homme-cobot. (INRS, 2020b)
Identifier et évaluer les limites et risques de la robotique collaborative
Les robots collaboratifs ont plusieurs limitations par rapport aux robots industriels « classiques » :
- Ils sont, pour le moment, moins précis et moins rapides.
- Ils ne sont généralement pas capables de manipuler des charges lourdes en raison de leur poids réduit afin de limiter les risques d’accident lors d’un éventuel contact avec l’opérateur.
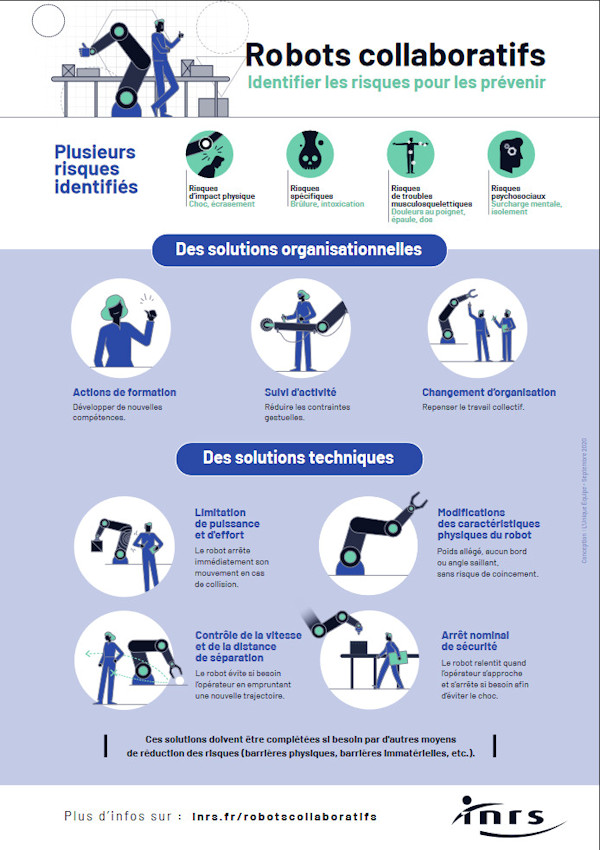
Source : INRS. (2020c)
Solutions techniques pour réduire les risques
Tous les robots utilisés au travail doivent répondre aux exigences de la norme NF EN ISO 10218 partie 1 et partie 2 de 2011 qui définissent les exigences de sécurité relatives aux robots industriels. Celles-ci indiquent les principes techniques combinables entre eux et à choisir en fonction de la situation :
Toutefois, ces fonctions ne permettent pas de réduire les autres risques d’impacts physiques ou spécifiques aux équipements. La mise en œuvre d’un robot collaboratif ne dispense donc pas de recourir à des barrières de protection, matérielles ou immatérielles (dispositifs scrutateurs, par exemple).
Solutions organisationnelles
Ces solutions techniques doivent être associées à des solutions organisationnelles :
- développement de nouvelles compétences dans la mise en œuvre des équipements y compris la maintenance de 1er niveau ;
- évaluation et évolution des sollicitations physiques et psychosociales ;
- adaptation du travail demandé, modification du poste de travail, réaménagement du travail collectif.
Risques et sécurité des opérateurs lors des interactions hommes-robots
Types de contacts potentiels lors des interactions hommes-robots
Il y a deux contacts potentiels qui peuvent se produire entre un opérateur et un robot.
- Quasi-statique : lorsque la partie du corps d’un opérateur peut se coincer entre la partie mobile du robot et une autre partie fixe ou mobile du système robotique.
- Contact transitoire : lorsque la partie du corps de l’opérateur ne se serre pas, ce qui signifie que l’opérateur peut rapidement se retirer ou reculer de la partie mobile du système robotique.
Evaluation des risques
Un danger est une condition susceptible de causer un dommage ou une blessure à un opérateur, ou d’endommager le système robotique ou l’environnement. Une évaluation des risques est une évaluation des tâches et des dangers associés sur la base de trois critères :
- Gravité de la blessure
- Exposition
- Évitement
1/ La gravité d’une blessure représente le degré de préjudice possible pour un opérateur.
Les conséquences du danger vont de S1 à S3.
- L’indice S1 représente une blessure faible et grave.
- Le score S2 représente une sévérité modérée.
- S3 représente un niveau de gravité élevé.
2/ Une exposition, associée à la fréquence ou à la durée, représente la probabilité qu’un opérateur soit exposé à un danger.
- La cote E1 représente une faible exposition à une activité occasionnelle.
- E2 représente une forte exposition à une routine ou à une opération continue.
- E0 est une option pour la vérification et la validation des mesures de réduction des risques.
3/ L’évitement représente la capacité d’un opérateur à détecter et à éviter le mode de défaillance ou le danger potentiel.
- A1 représente un évitement possible lorsque l’espace est suffisant pour s’écarter du chemin et que le temps de réaction est adéquat.
- A2 représente un dégagement insuffisant pour s’écarter du chemin et un contrôle de la vitesse réduite est utilisé. La cote A2 ne présente pas un temps de réaction suffisant.
- A3 représente un dégagement insuffisant pour s’écarter du chemin et la vitesse de contrôle réduite n’est pas utilisée. Un incident A3 tel qu’une explosion a un temps de réaction presque nul.
Raisons pour lesquelles un incident de sécurité lié au robot peut se produire
Il existe trois grandes catégories de raisons pour lesquelles un incident de sécurité lié aux robots peut se produire :
- Un bras ou un équipement robotique provoque un accident, mettant un opérateur dans une situation à risque.
- Une pièce mécanique tombe en panne dans le système du robot.
- Il se peut que l’alimentation du robot soit incontrôlée.
Liste des causes profondes ou des sources de danger identifiées :
- L’interaction de l’homme avec un robot peut potentiellement provoquer un mouvement ou une réaction dangereuse ou imprévue du robot.
- Les erreurs de commande sont des défauts/bogues intrinsèques ou inhérents au système de commande. Ces erreurs peuvent également se trouver dans le logiciel du système du robot.
- Il y a accès non autorisé lorsque le personnel ne connaît pas les mesures de protection en place ou leur état d’activation.
- Une défaillance mécanique est propice à une opération inattendue ou à une défaillance de l’effecteur final. Les systèmes d’alimentation présentent de sérieux risques d’incendie causés par des signaux électriques perturbateurs.
- La conception d’une cellule robotique collaborative est essentielle. Si la conception ou l’agencement est inadéquat, cela peut entraîner des risques inhérents au système.
Une conception axée sur la sécurité
Principaux facteurs déterminant dans les forces de collision
Il existe trois facteurs principaux qui déterminent les forces de collision.
- Le couple moteur
- L’énergie cinétique du robot et la charge utile effective.
- La distance de décélération
L’inertie réfléchie est l’inertie du moteur et de la partie haute vitesse du réducteur de vitesse multipliée par le carré du rapport de transmission vu sur l’arbre de sortie du réducteur de vitesse.
Mesure des forces de collision statiques et dynamiques
L’université de Mayence, en Allemagne, a mis au point plusieurs mesures essentielles pour une machine capable d’appliquer des forces de collision statiques et dynamiques à diverses parties du corps humain.
- Force de serrage pour les conditions statiques
- Force d’impact pour les collisions dynamiques
- Pression pour la force par unité de surface
- Constante de compression pour la rigidité des différentes régions du corps
Cellules de travail collaboratives
Types de collaboration
- Collaboration directe : L’opérateur et le robot travaillent simultanément à la réalisation d’une même pièce.
- Collaboration indirecte : L’opérateur et le robot travaillent sur une même pièce mais leurs actions sont alternées.
- Partage d’espace de travail : L’opérateur et le robot effectuent des tâches distinctes pour lesquelles ils peuvent être amenés à partager leur espace de travail
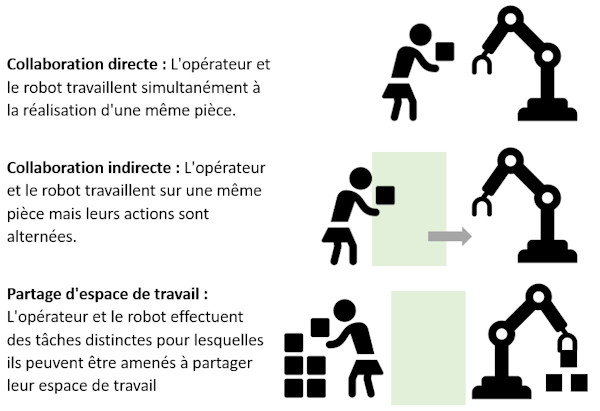
Types de collaborations homme-cobot d’après (Tihay & Perrin, 2018).
Classification des « îlots collaboratifs »
Le guide du CETIM sur la robotique collaborative (Acoulon, 2013, 2014) propose une classification des « îlots collaboratifs » en fonction de l’ordre croissant de l’interaction :
- Ilot robotisé standard : pas d’espace de travail commun excepté pour les phases de maintenance et nettoyage où le robot est à l’arrêt ;
- Ilot robotisé flexible : l’opérateur et le robot ne collaborent pas mais travaillent dans le même atelier (réduction des arrêts lors de la présence d’opérateurs) ;
- Ilot robotisé collaboratif : interaction ponctuelle ou quasi permanente selon les besoins ;
- Robot mobile : peut se déplacer de manière autonome dans l’atelier en présence d’opérateur(s), travaille sans intervention de l’opérateur ;
- Cobot : absence d’autonomie du bras, déplacement uniquement par action de l’opérateur.
Conception de cellules de travail robotisées
La conception d’une cellule cobot s’effectue en quatre étapes :
- Analyse et définition de la carte des tâches manuelles
- Commencez la carte des tâches robotiques
- Définir la carte des tâches de haut niveau
- Conception de la mise en page (et mettre à jour la carte des tâches)
La boîte à outils de conception de cellules de travail robotisées comprend les éléments suivants : problème, processus, méthode du chemin critique (CPM), disposition, simulation et alternatives de conception.
Chaque élément est essentiel pour concevoir efficacement une cellule de travail robotisée.
Défis de conception et d’optimisation des cellules robotisées
Les défis et les technologies clés de la conception et de l’optimisation des cellules robotisées sont les suivants :
- Sélection d’une configuration appropriée pour une tâche donnée
- Apprentissage des compétences manuelles et traduction
- Outil de conception collaborative
- Optimisation et ordonnancement de la disposition des cellules
- Conception optimale de l’outillage
- Collaboration homme-robot
Contenus associés
- Repères | Démarche ergonomique & robots collaboratifs – Partie 1 : Contexte
- Repères | Démarche ergonomique & Robots collaboratifs – Partie 2 : conduite de projet centrée sur l’activité
Ressources
Articles et guides
- Acoulon, S. (2014). Les robots collaboratifs—Guide d’intégration de la santé et de la sécurité. (Réédition). Centre technique des industries mécaniques (CETIM). https://bit.ly/3J2IB3h
- Atain-Kouadio, J. J., & Sghaier, A. (2017). Les robots et dispositifs d’assistance physique : Etat des lieux et enjeux pour la prévention (Note Scientifique et Technique NS 354). INRS. https://bit.ly/37asaEC
- Atain-Kouadio, J.-J., Sghaier, A., & Picot, D. (2015). Robots d’assistance physique : Fonctionnement et modes d’utilisation en industrie. Actes du 50ème Congrès de la Société d’Ergonomie de Langue Française (SELF), 560‑567. https://bit.ly/3wZVzwh
- INRS. (2020a). 10 questions sur les robots collaboratifs (ED 6386). INRS. https://bit.ly/3J4ruhm
- INRS. (2020b). Robots collaboratifs [Dossier thématique (PDF)]. INRS. https://bit.ly/3r2wWLB
- INRS. (2020c). Robots collaboratifs—Identifier les risques pour les prévenir [Infographie]. https://bit.ly/35zu2X9
- Jocelyn, S., Burlet-Vienney, D., Giraud, L., & Sghaier, A. (2017). Robotique collaborative. Evaluation des fonctions de sécurité et retour d’expérience des travailleurs, utilisateurs et intégrateurs au Québec (R-974 ; Rapports Scientifiques). IRSST Institut de recherche Robert-Sauvé en santé et en sécurité du travail. https://bit.ly/38noW1f
- Ministère du Travail. (2017). Guide de prévention à destination des fabricants et des utilisateurs—Pour la mise en œuvre des applications collaboratives robotisées. Ministère du Travail. https://bit.ly/3qBhQN5
- Tihay, D., & Perrin, N. (2018). Robotique collaborative : Perception et attentes des industriels. Hygiène et Sécurité au Travail, 250, 50‑57. https://bit.ly/3tLsHFV
- Vasic, M., & Billard, A. (2013). Safety issues in human-robot interactions. 2013 IEEE International Conference on Robotics and Automation, 197‑204. https://doi.org/10.1109/ICRA.2013.6630576
Normes
- NF EN 614-1+A1. (2009). Sécurité des machines – Principes ergonomiques de conception – Partie 1 : terminologie et principes généraux.
- NF EN 614-2+A1. (2008). Sécurité des machines – Principes ergonomiques de conception – Partie 2 : interactions entre la conception des machines et les tâches du travail.
- NF EN ISO 10218-1. (2011). Exigences de sécurité pour les robots industriels – Robots et dispositifs robotiques – Partie 1 : Robots.
- NF EN ISO 10218-2. (2011). Exigences de sécurité pour les robots industriels – Robots et dispositifs robotiques – Partie 2 : Système robot et intégration.
- NF EN ISO 11064-4. (2014). Conception ergonomique des centres de commande – Partie 4 : agencement et dimensionnement du poste de travail.
- NF EN ISO 13482. (2014). Robots et composants robotiques – Exigences de sécurité – Robots non médicaux pour les soins personnels.
- NF ISO 8373. (2012). Robots et composants robotiques – Vocabulaire – Robots manipulateurs industriels.
- ISO 12100. (2010). Sécurité des machines — Principes généraux de conception — Appréciation du risque et réduction du risque. Afnor EDITIONS. https://bit.ly/3xjC4z9
- ISO 9241-210. (2010). Ergonomie de l’interaction homme-système — Partie 210: Conception centrée sur l’opérateur humain pour les systèmes interactifs.
- ISO 9241-910. (2011). Ergonomie de l’interaction homme-système — Partie 910: Cadre pour les interactions tactiles et haptiques.
- ISO 9283. (1998). Manipulating industrial robots — Performance criteria and related test methods.
- ISO/TR 16982. (2002). Ergonomics of human-system interaction — Usability methods supporting human-centred design.
- ISO/TS 15066. (2016). Robots and robotic devices — Collaborative robots.
Crédit photo : Ars Electronica